Every time you drink from a water bottle or play with a toy, chances are you’re using something made through the process of plastic injection molding. Universal Plastic Mold houses all kinds of machines for this process so that we can meet your product development needs quickly and efficiently. Read on American Plastic Molds for more information.
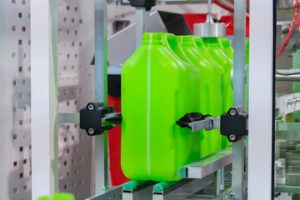
Family molds are perfect for applications that require multiple variations of one part. This allows for more efficient use of material by reducing the amount of sprues, runners and gates needed.
The quality of plastic products is mainly determined by the design of molds. Whether the finished product is a car part or an artificial leg, it must be strong and safe to use. It is also important to choose the right materials for the job. For example, corrosion-resistant steels are often used for medical equipment, while low-carbon martensitic aging steel is preferred in the manufacture of automotive parts and tools.
Injection molding is one of the most common methods for producing molded plastics. A powder or liquid polymer is injected into the cavity of the mould using a heated barrel and reciprocating screw. This method allows for high production rates and can be used to create complex shapes with high tolerances. The plastic is then cooled and the mould opened to release the finished product.
The design of the plastic injection mould is an essential factor in ensuring that the plastic products are produced correctly. This includes the guiding system, which helps to ensure that the molded plastic will be removed without any damage. This is a complex system that comprises a variety of components, such as ejector pins, locking blocks, and positioning structures. It is also necessary to consider the design of the ejection mechanism, which will help to ensure that the finished plastic part can be pushed out of the mould.
There are many different types of plastic injection molds, and the type that is best for a particular project depends on several factors. For example, a single-cavity mold can produce just one product per cycle, while a multi-cavity mold can produce several copies of the same part in the same process.
Other considerations include the complexity of the product and the type of material to be used. For example, some materials require a greater degree of re-heating and melting to achieve the correct properties. In addition, the granularity of the raw material must be taken into account.
Plastic molds are made from a wide range of materials, including alumina, copper, aluminium, steel, and phenolic. The best choice for a particular project will depend on the design, price, and durability requirements. In general, a higher cost will be associated with more complicated designs and materials.
Materials
Injection molding is the most common method of producing plastic parts. It is used in a variety of products from car parts to surgical tools and can often replace traditional metal parts. This is due to the fact that a reasonably designed plastic part can be cheaper and more durable than its metal counterparts. It is also much easier to produce complex shapes with plastics than metals, and they do not rust or oxidize easily.
The most common type of injection molding material is polyethylene (PE). PE can be molded into a variety of textures, shapes, and colors using different methods. It is an inexpensive, durable, and flexible material that can withstand high temperatures and is also moisture-resistant. It is available in a number of grades, including low-density (LDPE), high-density (HDPE), and polyethylene terephthalate (PET).
Another common plastic material is polycarbonate (PC). This is a strong and durable material that can withstand a lot of deformation without breaking. It is also a transparent material, and it can be produced in a range of colors and textures. It is an excellent choice for products that require durability and flexibility, such as protective cases.
Other types of injection molding materials include polypropylene, acrylonitrile butadiene styrene (ABS), ethylene-vinyl acetate (EVA), polyethylene naphthalate (PEN), and polyvinyl chloride (PVC). These are all durable plastics that can be molded into a variety of colors, textures, and shapes using various processes.
Plastics can also be mixed with other materials to create unique and useful features in products such as combining a soft touch material like rubber or adding colour. This is known as two-shot injection moulding and can be a very effective way to add functionality to a product.
The basic structure of a mold can vary depending on the type of plastic and the complexity of the product, but it typically includes a pouring system, temperature regulating system, molding parts, and structural parts. The structural parts are in direct contact with the plastic and must be carefully designed to ensure a high level of accuracy and long lifespan.
Tooling
The tooling that goes into a plastic mold is crucial to the quality and cost of a finished part. Depending on the complexity of the mold, there are different types of tooling to choose from. Choosing the right type of tooling can reduce the chances of defects and problems during production. In addition, proper maintenance and monitoring of the tooling can reduce the risk of errors and save time.
The injection mold tooling includes a number of components to ensure proper flow and pressure of the molten plastic during production. These include the sprue bush, gates, vents, and cooling channels. The sprue bush is the primary passage for the molten plastic from the injection nozzle to the mold cavity, and it has a significant impact on injection flow and pressure. The sprue bush must be designed to the precise specifications of the material and injection pressure.
Gates are a critical aspect of injection molding, as they control the flow and amount of plastic into the cavity. A properly placed gate can help to prevent flashing and shrinkage, and it can also make the molded part look more attractive. The gate must also be sized appropriately for the injection process. If it is too small, the plastic may not be packed sufficiently to fill the cavity (also known as a short shot). If it is too large, it can result in an overflow of plastic that is difficult to remove from the mold.
Other injection mold features, such as negative draft angles, thin-walled sections, and ribs, can require special tools or inserts to enable proper injection and ejection of the plastic parts. These parts also need effective cooling channels to prevent warping and sink marks.
A quick plastic injection tool is a low-volume prototype tool that is typically made through 3D printing, machining, or cast urethane. This type of tool is useful in the early stages of product development, as it allows engineers and designers to troubleshoot their design before the actual injection molding process begins. This can minimize errors and costs in the manufacturing process, saving time and money for the company and customer. Once the design is finalized, this type of prototype can be replaced with a dedicated or quick die change tool for full production.
Production
After a plastic product is designed by an industrial designer or engineer, a mould, which is made of metal, typically steel or aluminium, is precision-machined to form the features that will be molded. The injection molding process is used to produce a wide variety of products, from the smallest component to a car body panel. The mould is clamped together and molten plastic injected under high pressure to fill the cavity. Once the plastic has cooled and solidified, the mold opens and the finished part is ejected.
The type of plastic that is injected into the mold depends on the application. Some common plastics are ABS (acrylonitrile butadiene styrene), which is hard and durable, and HDPE (high-density polyethylene), which is both lightweight and strong. A typical injection mold has movable side actions and pulls to create undercuts, and machined inserts to support and shape complex parts. It also has cooling channels to reduce cycle times and an electronic sensor to monitor pressures and temperatures.
Injection plastic molds are expensive tools, so they must be cared for to extend their life. Several factors contribute to plastic mold wear, including abrasion, friction, temperature and chemical corrosion. Injection molds are often lubricated with a release agent to reduce friction between the plastic and the tool. This is especially important during the injection process, when the plastic is molten and may stick to the tool if not adequately lubricated.
Another way that plastic is molded is through extrusion, which uses high temperatures and rotational movement to coat the inside of a hollowed out shape with liquid plastic. This is a very efficient manufacturing process because little to no material is wasted and the liquid plastic can be formed into many different shapes with one mould. For example, the liquid plastic is pressed through a die that has been custom made for the desired outcome. This is a good option for large, hollow parts like tanks and bins. It is also a popular choice for making pet houses, kayaks and road cones because it is cheaper than other methods of plastic moulding.